What is cutting speed, feed and depth of cut?
Cutting speed, is a critical parameter in machining processes that refers to the speed at which the cutting tool passes over the surface of the material being cut, it is also known as surface speed.
Cutting speed definition (Vc): The speed at which the material is removed by the cutting tool. It is the tangential speed of the workpiece surface relative to the cutting tool.
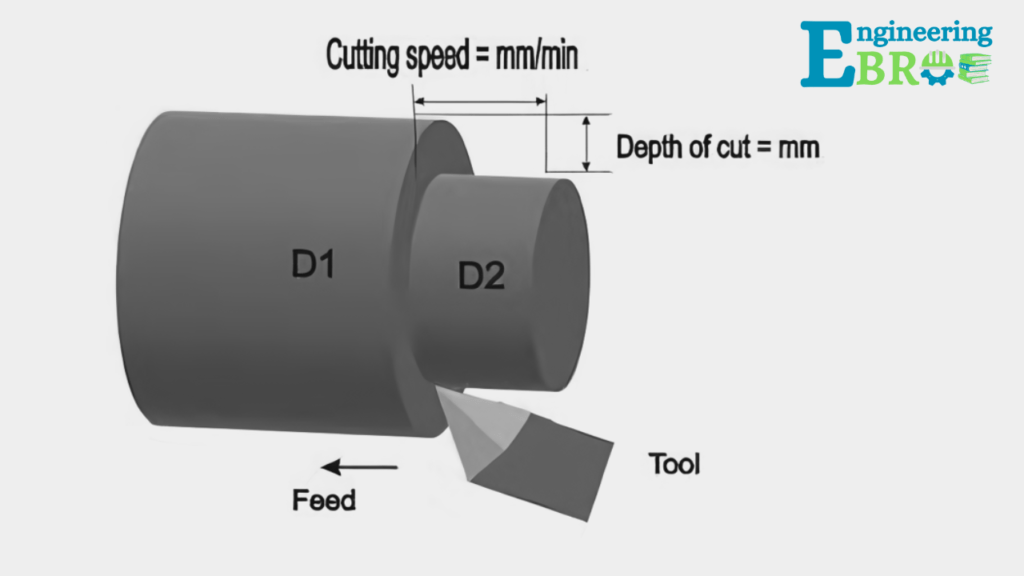
Cutting speed unit?
It is typically measured in surface feet per minute (sfm) or meters per minute (m/min)
Feed Rate (F): The linear distance that the cutting tool travels per minute or per revolution of the spindle.
Feed rate units?
Linear Feed Rate: Measured in mm/min or in/min.
Revolutionary Feed Rate: Measured in mm/rev or in/rev.
Depth of Cut (d): The distance the cutting tool penetrates below the original surface of the workpiece during machining,
Depth of cut units?
usually measured in millimeters (mm) or inches (in).
Table of Contents
Why Cutting speed is important?
Cutting-speed is a critical parameter in machining processes for several reasons, impacting tool life, surface finish, production efficiency, and overall machining quality. Here are the key reasons why cutting speed is important:
Tool Life
Optimal cutting-speed can maximize tool life.
- Heat Generation: Cutting-speed affects the amount of heat generated at the cutting interface. Too high a speed can generate excessive heat, leading to rapid tool wear or even failure.
- Wear Rates: Different materials have optimal cutting speeds that minimize wear. Operating at or near these speeds can significantly extend tool life.
Surface Finish
Cutting speed influences the quality of the surface finish.
- Smoothness: Appropriate cutting-speeds can reduce surface roughness, leading to smoother finishes. Higher speeds can often improve the finish, but only up to a point before negative effects set in.
- Consistency: Consistent cutting-speeds help maintain uniformity in surface finish across multiple parts.
Production Efficiency
Higher cutting speeds can improve production efficiency.
- Material Removal Rate: Increased cutting-speeds often lead to higher material removal rates, reducing the time required to machine a part.
- Cycle Time: By reducing cycle times, higher cutting speeds can enhance overall production throughput and efficiency.
Machining Costs
Optimizing cutting speed can reduce machining costs.
- Tool Costs: Prolonged tool life reduces the frequency of tool changes and replacements, cutting down on tool costs.
- Operational Costs: Efficient machining reduces machine time and energy consumption, contributing to lower operational costs.
Workpiece Integrity
Proper cutting speeds can preserve the integrity of the workpiece.
- Minimize Deformation: Incorrect speeds can cause workpiece deformation due to excessive heat or mechanical forces. Proper speeds help maintain the desired dimensional accuracy and mechanical properties.
- Prevent Damage: Operating at appropriate speeds reduces the risk of workpiece damage, such as burns or micro-cracks, which can compromise part quality.
Compatibility with Tool Material
Cutting-speeds must be matched to the tool material.
- Tool Material Properties: Different tool materials (e.g., high-speed steel, carbide, ceramics) have different optimal speed ranges. Using the correct speed for the tool material ensures efficient cutting and prolongs tool life.
- Heat Resistance: Advanced tool materials like carbide can withstand higher speeds compared to high-speed steel, allowing for faster machining without compromising tool life.
Safety
Maintaining correct cutting speeds is crucial for safe machining operations.
- Tool Breakage: Excessive cutting-speeds can lead to sudden tool breakage, posing safety hazards to operators.
- Stable Operation: Proper speeds ensure stable cutting conditions, reducing the risk of machine vibrations or chatter that can lead to accidents.
Practical Example:
Consider machining a mild steel part using a carbide tool. The recommended cutting speed for mild steel with a carbide tool might be around 150 m/min.
If the machinist sets the speed significantly lower than this (e.g., 50 m/min), the tool might wear out prematurely due to built-up edge formation, and the surface finish could be poor.
Conversely, setting it too high (e.g., 300 m/min) could cause excessive heat, leading to rapid tool wear or even tool failure.
By setting the cutting speed to the recommended 150 m/min, the machinist can achieve a balance between efficient material removal, good surface finish, and extended tool life, optimizing the overall machining process.
Types of cutting speed for different materials?
For Aluminum: 300-600 sfm (91-183 m/min)
For Mild Steel: 100-150 sfm (30 – 45 m/min)
For Hardened Steel: 50-100 sfm (15 – 30 m/min)
It can vary depending upon the cutting tool material too so
Checkout – Cutting-speed calculator to know the best cutting speed and feed for other materials
Cutting speed formula?
Cutting speed can be calculated using the following formula:
Vc = pi * D *N / 1000
where:
– Vc = Cutting speed (m/min or sfm)
– D = Diameter of the workpiece (mm or inches)
– N = Spindle speed (rpm)
– Pi = 3.14
How to calculate cutting speed of lathe machine?
To calculate the cutting-speed in a machining process, you can use the
Step-by-Step Example:
Given:
– Diameter of the workpiece D = 100 mm
– Spindle speed N = 600 rpm
Calculate Cutting Speed Vc:
1.Identify the variables:
– D = 100mm
– N = 600 rpm
2.Plug the values into the formula:
Vc = pi * 100 * 6001000}
3. Perform the calculation:
Vc = 3.1416 * 100 * 600 / 1000
Vc = 188496 / 1000
Vc = 188.496 m/min
So, the cutting-speed is approximately 188.5 m/min.
Another Example in Imperial Units:
If the diameter is given in inches and the desired cutting speed is in surface feet per minute (sfm), use the formula:
Vc = pi * D * N / 12
Given:
– Diameter of the workpiece D = 4 inches
– Spindle speed N = 800 rpm
Calculate Cutting-Speed Vc:
1. Identify the variables:
( D = 4 ) inches
( N = 800 ) rpm
2. Plug the values into the formula: Vc = pi * 4 * 800 / 12
3. Perform the calculation: Vc = 3.1416 * 4 * 800 / 12
Vc = 10048/12
Vc = 837.333 sfm
So, the cutting-speed is approximately 837.3 sfm.
Practical Considerations:
– Material: Different materials require different cutting-speeds. Always refer to recommended cutting speed charts based on the material of the workpiece and the tool.
– Tool Material: The cutting tool material also affects the optimal cutting-speed. Carbide tools can usually handle higher speeds than high-speed steel (HSS) tools.
– Coolant: Using a coolant can allow for higher cutting speeds by reducing heat and friction.
By using these formulas and considering the practical aspects, machinists can determine the optimal cutting speed for their specific machining conditions.
Factors that effect cutting speed?
Several factors influence the cutting-speed in machining operations, each playing a significant role in determining the optimal speed for a given situation. Here are the key factors:
1. Workpiece Material
- Hardness: Harder materials generally require slower cutting speeds to prevent excessive tool wear and heat generation.
- Toughness: Tough materials can cause more wear and may necessitate slower speeds.
- Thermal Conductivity: Materials with low thermal conductivity require lower cutting-speeds to manage heat effectively.
2. Tool Material
- Tool Composition: Different tool materials (e.g., high-speed steel, carbide, ceramics) have different optimal cutting speeds.
- Coating: Coatings on tools (e.g., TiN, TiAlN) can allow for higher cutting-speeds by reducing friction and wear.
- Tool Geometry: The shape and design of the cutting tool, including rake angle and clearance angle, affect the cutting speed.
3. Machining Conditions
- Spindle Speed: Higher spindle speeds can increase the cutting-speed but must be balanced against the tool’s and material’s capabilities.
- Feed Rate: The rate at which the tool advances affects the cutting-speed. Higher feed rates generally require lower cutting speeds to manage heat and tool wear.
- Depth of Cut: Deeper cuts generate more heat and stress, often requiring lower cutting speeds.
4. Cooling and Lubrication
- Coolant Use: Proper application of coolants can allow for higher cutting-speeds by dissipating heat.
- Lubrication: Reducing friction with appropriate lubricants can permit higher speeds.
5. Machine Tool Capabilities
- Power and Rigidity: More powerful and rigid machines can handle higher cutting-speeds without excessive vibration or deflection.
- Precision and Stability: Machines with better precision and stability can operate at higher speeds effectively.
6. Type of Operation
- Turning, Milling, Drilling: Each machining operation has different optimal cutting-speeds. For example, milling often uses higher speeds than turning.
- Roughing vs. Finishing: Roughing operations, which remove more material, typically use lower cutting-speeds compared to finishing operations, which focus on surface quality.
7. Environmental Factors
- Temperature: Ambient temperature can affect cutting-speeds, with higher temperatures possibly requiring adjustments to manage heat.
- Workpiece Clamping: Secure clamping and fixturing can allow for higher speeds by preventing movement and vibration.
8. Tool Wear
- Tool Condition: Worn tools require lower cutting-speeds to maintain effectiveness and prevent further damage.
- Tool Change Intervals: Frequent tool changes can necessitate adjustments in cutting speeds to balance tool life and productivity