In this blog, we will know the 11 types of lathe machines and understand the specifications of each types of lathe machines,
Actually, there are 8 types of lathe but by considering the subtypes there are generally 11 types of lathe machines
2 out of 3
[bottom_button]
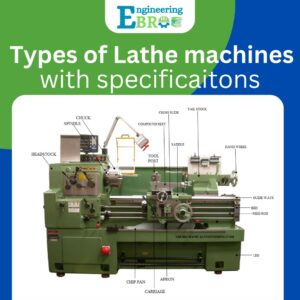
List of types of lathe machines
- Speed lathe
- Engine lathe
- Bench lathe
- Toolroom lathe
- Automatic lathe
- Semi Automatic lathe
- Turret lathes
- capstan lathe
- Turret lathe
- Special Purpose lathe
- Gap bed lathe
- wheel lathe
- axle lathe
Also Read – Lathe Machine – Purpose, Parts, Working, Types Specifications
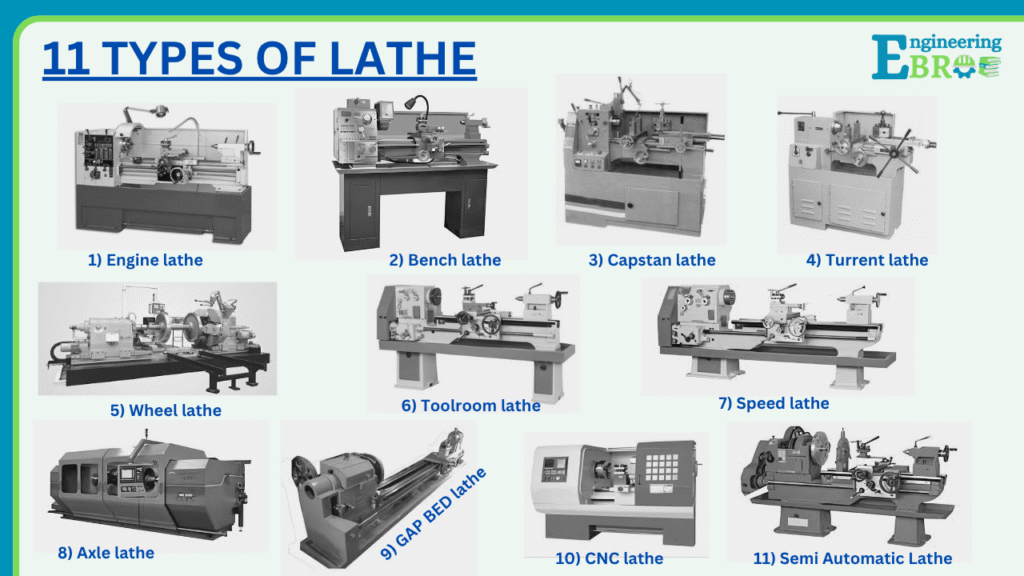
Table of Contents
Follow us on Facebook
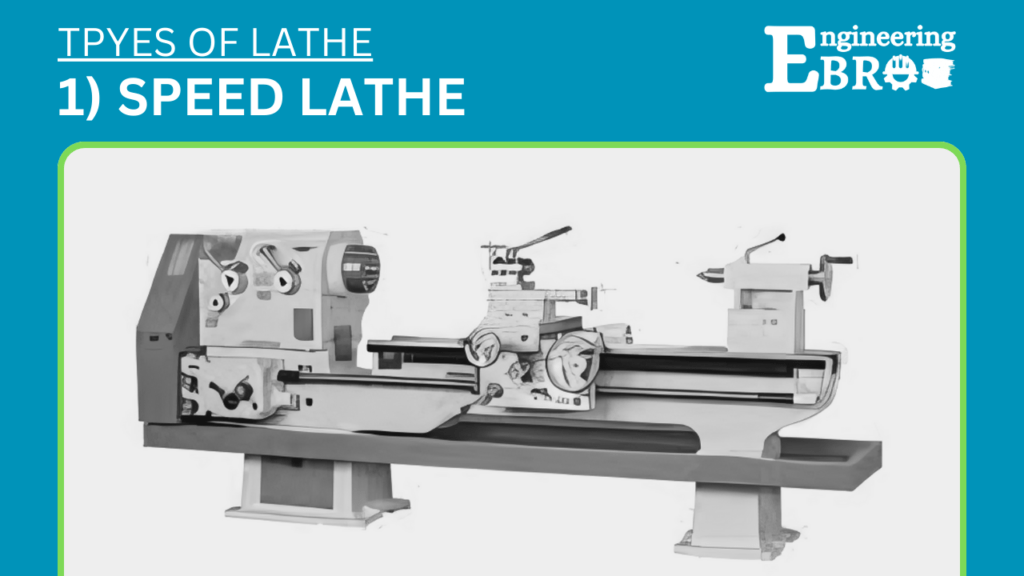
Speed lathe
A speed lathe, also known as a wood-turning lathe, is one of the types of lathe machines that is primarily used for woodworking and some light metalworking tasks. It is characterized by its simplicity and the high speed at which it operates. Speed lathes are typically used for operations such as woodturning, spinning, centering, and polishing.
Specifications of a Speed Lathe
- Bed Length:
- Typically ranges from 24 inches to 48 inches, depending on the model.
- Swing Over Bed:
- This refers to the maximum diameter of the workpiece that can be turned over the bed. It commonly ranges from 6 inches to 12 inches.
- Distance Between Centers:
- Indicates the maximum length of the workpiece that can be held between the headstock and tailstock. Typically, it ranges from 15 inches to 36 inches.
- Spindle Speed:
- Speed lathes generally operate at high speeds, often ranging from 1,000 RPM to 4,000 RPM. Some models have variable speed controls.
- Motor Power:
- Typically ranges from 0.5 HP to 2 HP, depending on the size and capacity of the lathe.
- Tailstock:
- The tailstock can be moved along the bed and is used to support the end of the workpiece with a center or for drilling operations.
- Tool Rest:
- An adjustable rest where the operator places the cutting tools. It can be moved and locked in position as required.
- Construction Material:
- Usually made from cast iron or steel to provide stability and minimize vibrations during operation.
- Overall Weight:
- Can vary from 50 pounds to several hundred pounds, depending on the size and construction material.
- Bed Type:
- The bed can be either flat or tubular. Flatbeds are more common in metalworking lathes, while tubular beds are more common in wood lathes.
- Additional Features:
- Some speed lathes come with additional features such as digital readouts for speed, reverse operation, and various attachments for different turning tasks.
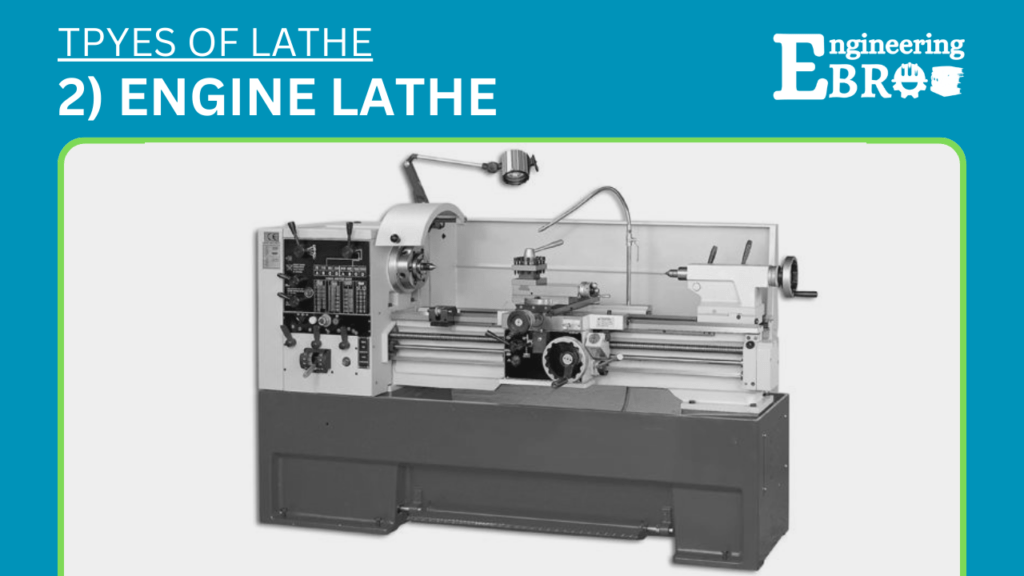
Engine lathe
An engine lathe, also known as a center lathe, is one of the types of lathe machines which is versatile and widely used machine tool designed primarily for machining cylindrical parts. It can perform a variety of operations such as turning, facing, drilling, threading, and more. Engine lathes are commonly used in metalworking, but they can also be adapted for wood or plastic workpieces.
Specifications of an Engine Lathe
- Bed Length:
- Typically ranges from 36 inches to 120 inches or more, depending on the model and intended use.
- Swing Over Bed:
- Indicates the maximum diameter of the workpiece that can be machined. Common ranges are from 12 inches to 24 inches.
- Distance Between Centers:
- Refers to the maximum length of the workpiece that can be held between the headstock and tailstock. Usually ranges from 24 inches to 60 inches, with larger industrial models having even greater capacities.
- Spindle Speed:
- Engine lathes usually have multiple speed settings. Typical speeds range from 20 RPM to 2,500 RPM, often controlled via a gearbox or variable speed drive.
- Motor Power:
- Motor power ranges from 1 HP for smaller lathes to over 20 HP for large industrial models.
- Tailstock:
- The tailstock can move along the bed and is used to support the end of the workpiece or to hold tools for drilling, reaming, etc. It typically has a quill travel of 4 to 6 inches.
- Tool Post:
- The tool post holds the cutting tools and can be adjusted and rotated for precise tool positioning. Quick-change tool posts are common for efficiency.
- Carriage:
- The carriage moves along the bed and carries the cutting tool. It includes the cross-slide, compound rest, and apron.
- Lead Screw:
- Used for threading operations, the lead screw engages with the carriage to produce precise threads.
- Feed Rod:
- Used for automatic feed operations during turning and facing.
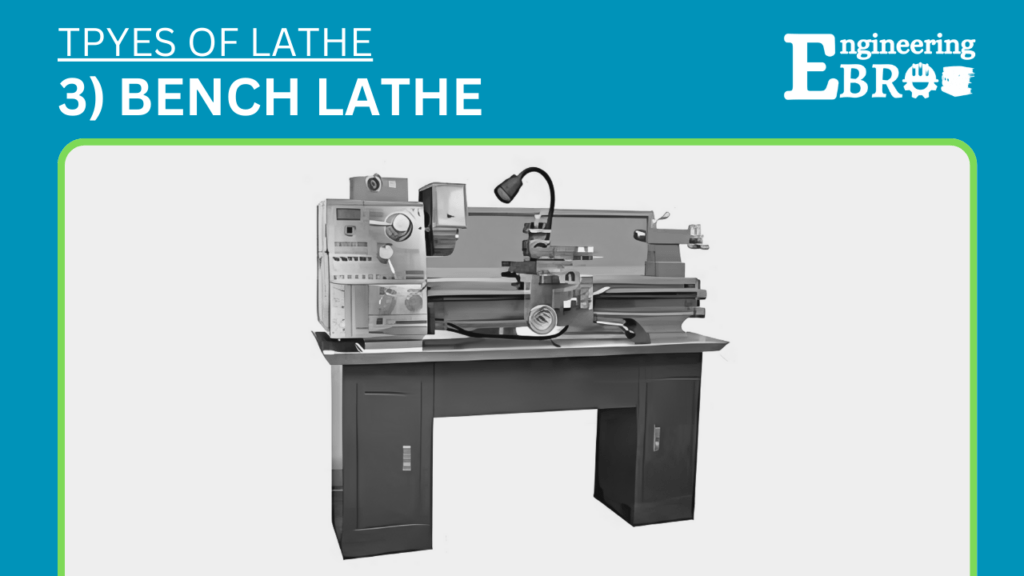
Bench lathe
A bench lathe, also known as a benchtop lathe, is a smaller and one of the more compact types of lathe machines designed to be mounted on a workbench. It is ideal for small-scale machining tasks and is commonly used in workshops, educational settings, and for hobbyist purposes. Bench lathes are versatile machines capable of performing various operations such as turning, drilling, facing, and threading.
Specifications of a Bench Lathe
- Bed Length:
- Typically ranges from 20 inches to 40 inches, depending on the model.
- Swing Over Bed:
- This is the maximum diameter of the workpiece that can be machined. Commonly ranges from 7 inches to 12 inches.
- Distance Between Centers:
- Refers to the maximum length of the workpiece that can be held between the headstock and tailstock. Typically ranges from 12 inches to 30 inches.
- Spindle Speed:
- Bench lathes usually have variable speed settings. Speeds often range from 100 RPM to 3,000 RPM, controlled either by manual gear changes or electronic speed control.
- Motor Power:
- Motor power typically ranges from 0.5 HP to 2 HP, suitable for small to medium-sized tasks.
- Tailstock:
- The tailstock is movable along the bed and used to support the end of the workpiece or hold drilling tools. It generally has a quill travel of 2 to 3 inches.
- Tool Post:
- The tool post holds the cutting tools and can be adjusted for precise tool positioning. Quick-change tool posts are often available.
- Carriage:
- The carriage includes the cross-slide and compound rest, providing movement for cutting tools along the bed and in the cross direction.
- Lead Screw:
- Used for threading operations and providing precise longitudinal movement of the carriage.
- Feed Rod:
- Utilized for automatic feed during turning and facing operations.
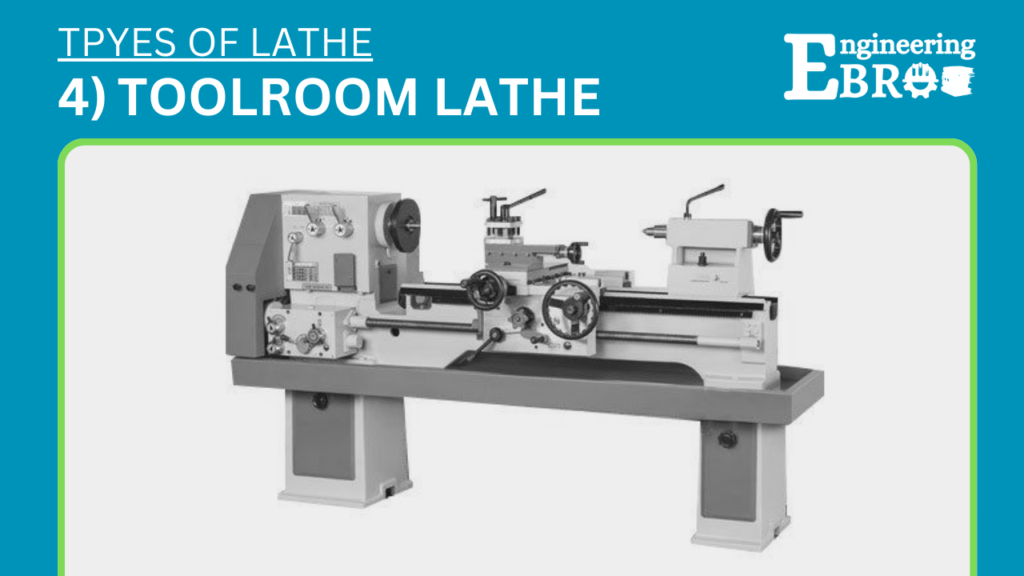
Toolroom lathe
A tool room lathe is a high-precision lathe used for intricate and detailed work, typically found in tool rooms, maintenance shops, and production environments. These lathes are designed for high accuracy and are often used for making jigs, fixtures, precision tools, and parts that require tight tolerances.
Specifications of a Tool Room Lathe
- Bed Length:
- Typically ranges from 36 inches to 80 inches, depending on the model.
- Swing Over Bed:
- Indicates the maximum diameter of the workpiece that can be machined. Commonly ranges from 10 inches to 20 inches.
- Distance Between Centers:
- Refers to the maximum length of the workpiece that can be held between the headstock and tailstock. Usually ranges from 24 inches to 60 inches.
- Spindle Speed:
- Tool room lathes generally have a wide range of spindle speeds, often from 30 RPM to 3,500 RPM, controlled via a variable speed drive or gear system.
- Motor Power:
- Motor power ranges from 1.5 HP to 10 HP, depending on the size and intended use of the lathe.
- Tailstock:
- The tailstock is movable along the bed and is used to support the end of the workpiece or hold tools for drilling, reaming, etc. It typically has a quill travel of 3 to 5 inches.
- Tool Post:
- The tool post holds the cutting tools and is highly adjustable for precise positioning. Often, quick-change tool posts are used for efficiency.
- Carriage:
- The carriage moves along the bed and carries the cross-slide, compound rest, and apron. It allows for precise movement and control of the cutting tool.
- Lead Screw:
- Used for threading operations, the lead screw engages with the carriage to produce precise threads.
- Feed Rod:
- Utilized for automatic feed during turning and facing operations.
Turret lathes
i) capstan lathe
A capstan lathe, also known as a turret lathe, is one of the types of lathe machines designed for the repetitive production of identical parts. It features a turret (capstan) that holds multiple tools, allowing for rapid tool changes and efficient machining processes. This makes it ideal for batch production and industrial settings where high productivity is essential.
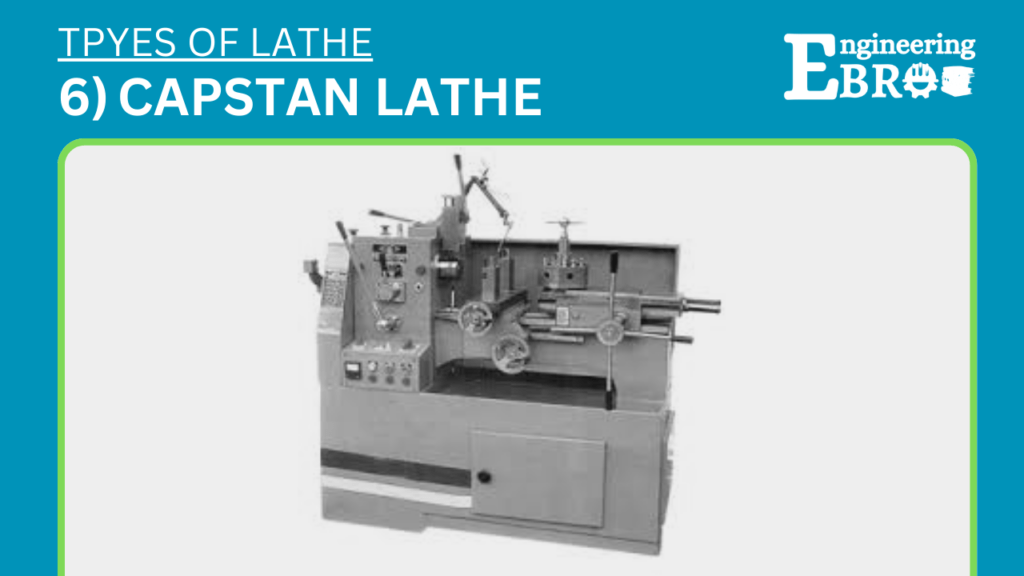
Specifications of a Capstan Lathe
- Bed Length:
- Typically ranges from 24 inches to 60 inches, depending on the model and intended use.
- Swing Over Bed:
- Indicates the maximum diameter of the workpiece that can be machined. Commonly ranges from 8 inches to 15 inches.
- Distance Between Centers:
- Refers to the maximum length of the workpiece that can be held between the headstock and the turret. Usually ranges from 12 inches to 40 inches.
- Turret Capacity:
- The number of tools that can be mounted on the turret. Generally ranges from 4 to 8 tools.
- Spindle Speed:
- Capstan lathes usually have a wide range of spindle speeds, often from 50 RPM to 3,000 RPM, controlled via a variable speed drive or gearbox.
- Motor Power:
- Motor power ranges from 1 HP to 7.5 HP, depending on the size and capacity of the lathe.
- Tailstock:
- Often replaced by the turret in capstan lathes, but some models may include a tailstock for specific operations.
- Carriage:
- The carriage is used for longitudinal movement along the bed. It typically includes a cross-slide and a compound rest.
- Cross-Slide:
- Allows for transverse movement and is often equipped with additional tool posts or holders.
- Construction Material:
- Typically made from high-grade cast iron or steel for stability and vibration reduction.
ii) Turret lathe
A turret lathe is one of the types of lathe machines which are metalworking lathes characterized by a rotating turret that holds multiple tools. This setup allows for quick changes between different machining operations, making turret lathes ideal for high-volume production and repetitive tasks. There are two main types of turret lathes: horizontal and vertical. Here, we’ll focus on the horizontal type, which is more common.
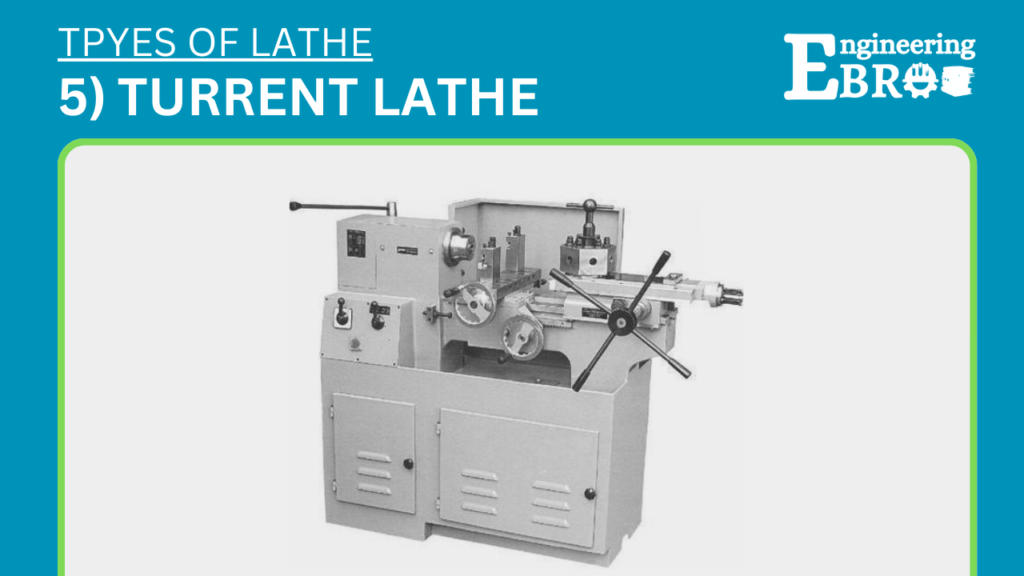
Specifications of a Turret Lathe
- Bed Length:
- Typically ranges from 24 inches to 60 inches or more, depending on the model and intended use.
- Swing Over Bed:
- Indicates the maximum diameter of the workpiece that can be machined. Common ranges are from 10 inches to 24 inches.
- Distance Between Centers:
- Refers to the maximum length of the workpiece that can be held between the headstock and the turret. Usually ranges from 24 inches to 60 inches.
- Turret Capacity:
- The number of tools that can be mounted on the turret. Generally ranges from 4 to 12 tools, depending on the model.
- Spindle Speed:
- Turret lathes usually have a wide range of spindle speeds, often from 50 RPM to 3,000 RPM, controlled via a variable speed drive or gearbox.
- Motor Power:
- Motor power ranges from 3 HP to 15 HP, depending on the size and capacity of the lathe.
- Tailstock:
- Many turret lathes replace the traditional tailstock with a turret, but some models may still include a tailstock for specific operations.
- Carriage:
- The carriage provides longitudinal movement along the bed and typically includes a cross-slide for transverse movement.
- Cross-Slide:
- Allows for transverse movement and often supports additional tool posts or holders.
- Tool Post:
- The tool post holds the cutting tools and can be quickly changed or adjusted. Turret lathes usually have multiple tool posts mounted on the turret.
Special Purpose lathe
i) Gap bed lathe
A gap bed lathe is one of the versatile types of lathe machines that features a removable section of the bed near the headstock. This design allows for machining of larger diameter workpieces that wouldn’t normally fit over the lathe’s bed. The gap bed lathe is commonly used in workshops where flexibility is required to handle a range of workpiece sizes.
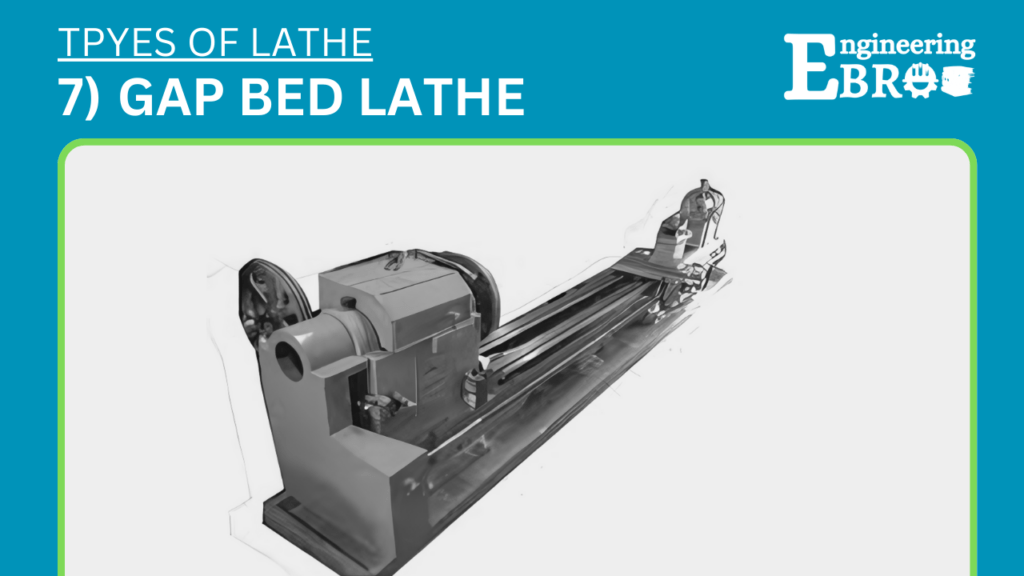
Specifications of a Gap Bed Lathe
- Bed Length:
- Typically ranges from 40 inches to 80 inches, but can be longer for industrial models.
- Swing Over Bed:
- Indicates the maximum diameter of the workpiece that can be machined without removing the gap. Commonly ranges from 10 inches to 24 inches.
- Swing Over Gap:
- The maximum diameter of the workpiece that can be machined when the gap section is removed. This often ranges from 18 inches to 40 inches, depending on the size of the lathe.
- Swing Over Cross Slide:
- Refers to the maximum diameter of the workpiece that can be machined over the cross slide. Typically ranges from 6 inches to 12 inches.
- Distance Between Centers:
- Indicates the maximum length of the workpiece that can be held between the headstock and tailstock. Usually ranges from 24 inches to 60 inches, but can be longer for larger models.
- Spindle Speed:
- Gap bed lathes usually offer a wide range of spindle speeds, typically from 30 RPM to 2,500 RPM, controlled via a gearbox or variable speed drive.
- Motor Power:
- Motor power typically ranges from 2 HP to 10 HP, depending on the size and capacity of the lathe.
- Tailstock:
- The tailstock is movable along the bed and is used to support the end of the workpiece or hold tools for drilling, reaming, etc. It generally has a quill travel of 3 to 5 inches.
- Tool Post:
- The tool post holds the cutting tools and can be adjusted and rotated for precise tool positioning. Quick-change tool posts are common.
- Carriage:
- The carriage moves along the bed and carries the cross-slide and compound rest, allowing for precise movement and control of the cutting tool.
ii) wheel lathe
A wheel lathe is one of the types of lathe machines used primarily for machining railway wheels, locomotive wheels, and other large wheels. These lathes are designed to handle the significant size and weight of wheelsets and are essential for maintaining and refurbishing railway rolling stock. Wheel lathes can machine the entire wheel profile, including the flange and tread, ensuring proper shape and balance.
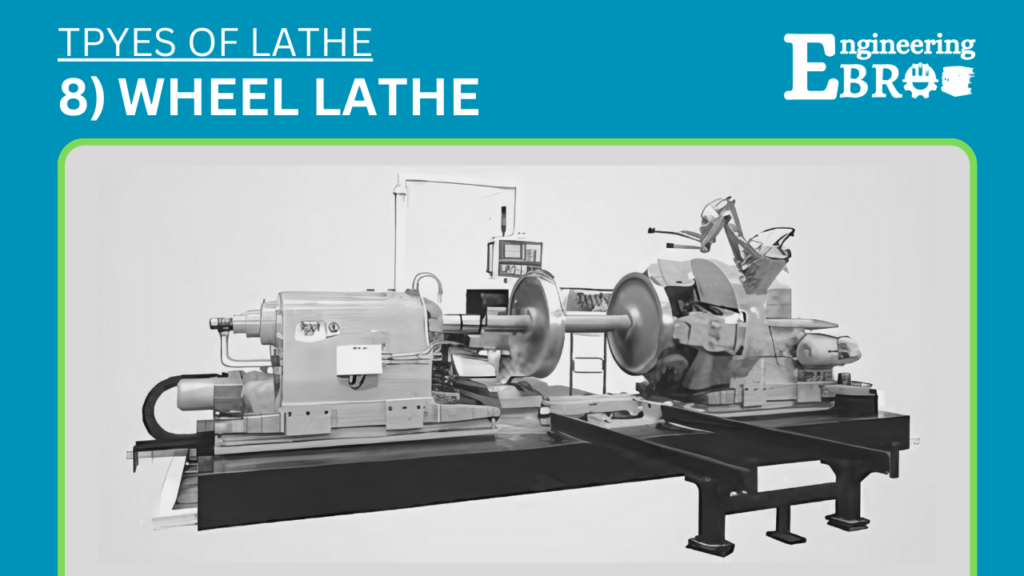
Specifications of a Wheel Lathe
- Swing Over Bed:
- Indicates the maximum diameter of the wheel that can be machined. Commonly ranges from 40 inches to 80 inches or more.
- Distance Between Centers:
- Refers to the maximum length of the axle that can be accommodated. Typically ranges from 60 inches to 120 inches, depending on the lathe size.
- Wheel Diameter Capacity:
- The range of wheel diameters that the lathe can handle. Typically ranges from 20 inches to 60 inches.
- Spindle Speed:
- Wheel lathes usually have a range of spindle speeds, typically from 10 RPM to 300 RPM, controlled via a variable speed drive or gearbox.
- Motor Power:
- Motor power ranges from 15 HP to 100 HP or more, depending on the size and capacity of the lathe.
- Tool Post:
- The tool post holds the cutting tools and is often designed to handle heavy-duty cutting operations. Turret tool posts or multiple tool posts are common.
- Carriage:
- The carriage moves along the bed and supports the cross-slide and tool post, allowing for precise control of the cutting tool. It is designed to handle the heavy loads associated with wheel machining.
- Cross-Slide:
- Allows for transverse movement of the cutting tool, essential for machining the wheel profile.
- Construction Material:
- Typically made from high-grade cast iron or steel to ensure stability and reduce vibrations during heavy-duty machining.
- Weight:
- Wheel lathes are very heavy, often weighing several tons due to the need to handle large and heavy wheel sets.
iii) Axle lathe
An axle lathe is a specialized machine designed for machining railway axles. These lathes are engineered to handle the significant size and weight of railway axles, ensuring precision in operations such as turning, facing, threading, and profiling. Axle lathes are crucial for maintaining and refurbishing axles to ensure the safety and efficiency of railway vehicles.
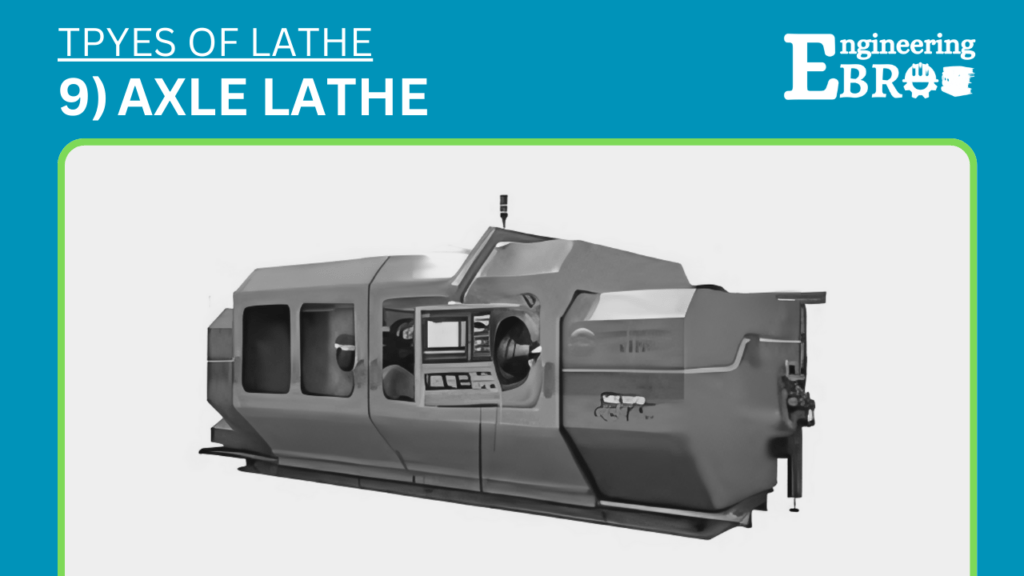
Specifications of an Axle Lathe
- Bed Length:
- Typically ranges from 80 inches to 160 inches or more, depending on the model and intended use.
- Swing Over Bed:
- Indicates the maximum diameter of the axle that can be machined. Commonly ranges from 16 inches to 36 inches.
- Distance Between Centers:
- Refers to the maximum length of the axle that can be accommodated. Usually ranges from 80 inches to 140 inches.
- Spindle Speed:
- Axle lathes usually have a range of spindle speeds, typically from 10 RPM to 500 RPM, controlled via a variable speed drive or gearbox.
- Motor Power:
- Motor power ranges from 20 HP to 100 HP or more, depending on the size and capacity of the lathe.
- Tool Post:
- The tool post holds the cutting tools and is designed to handle heavy-duty cutting operations. Turret tool posts or multiple tool posts are common.
- Carriage:
- The carriage moves along the bed and supports the cross-slide and tool post, allowing for precise control of the cutting tool. It is designed to handle the heavy loads associated with axle machining.
- Cross-Slide:
- Allows for transverse movement of the cutting tool, essential for machining various profiles on the axle.
- Construction Material:
- Typically made from high-grade cast iron or steel to ensure stability and reduce vibrations during heavy-duty machining.
- Weight:
- Axle lathes are very heavy, often weighing several tons due to the need to handle large and heavy axles.
[middle_button link=”https://drive.google.com/drive/folders/1JKHHA6pCfxLgSmvpKKUBUYvIWwCF8-No”]
Automatic lathe or CNC lathe
An automatic lathe is one of the types of lathe machines which are high-production machines designed to automatically perform repetitive turning operations on small to medium-sized workpieces. These lathes are ideal for mass production, providing high efficiency and consistency. Automatic lathes can be categorized into different types, such as single-spindle, multi-spindle, and Swiss-type lathes. Here, we’ll focus on the general specifications for a typical automatic lathe.
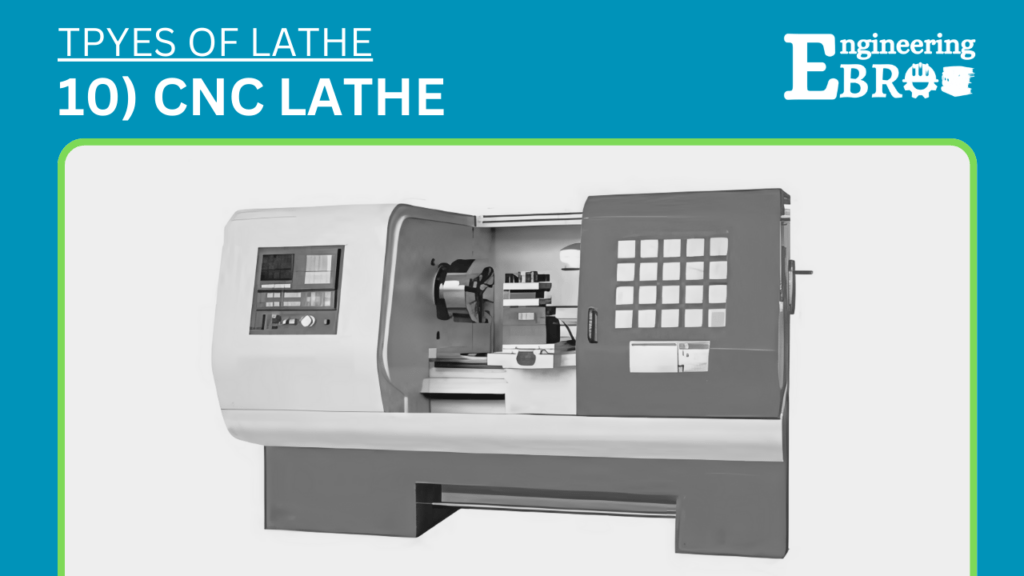
Specifications of an Automatic Lathe
- Type:
- Single-spindle or multi-spindle, CNC or cam-operated.
- Max Workpiece Diameter:
- Typically ranges from 5 mm to 50 mm, depending on the model and application.
- Max Workpiece Length:
- Generally ranges from 20 mm to 300 mm.
- Spindle Speed:
- Automatic lathes usually have a wide range of spindle speeds, often from 500 RPM to 10,000 RPM, controlled via a variable-speed drive or gearbox.
- Number of Spindles:
- Single-spindle or multi-spindle (up to 8 spindles).
- Number of Tool Stations:
- Typically ranges from 4 to 12 tool stations, allowing for various operations like turning, drilling, threading, and milling.
- Motor Power:
- Motor power ranges from 2 HP to 15 HP, depending on the size and capacity of the lathe.
- Control System:
- CNC controls for modern automatic lathes, with options for manual or cam-controlled versions for older models.
- Turret Type:
- Turrets can be indexed automatically, allowing for quick tool changes and multiple operations in a single setup.
- Feed Mechanism:
- Automatic bar feeders or magazine loaders for continuous operation without manual intervention.
Semi Automatic lathe
A semi-automatic lathe is one of the types of lathe machines that combines manual operation with automated features, offering versatility and efficiency for various machining tasks. These lathes are often used in workshops and small-scale manufacturing settings where operators need some degree of control over the machining process while benefiting from automated functions. Here are the specifications for a typical semi-automatic lathe:
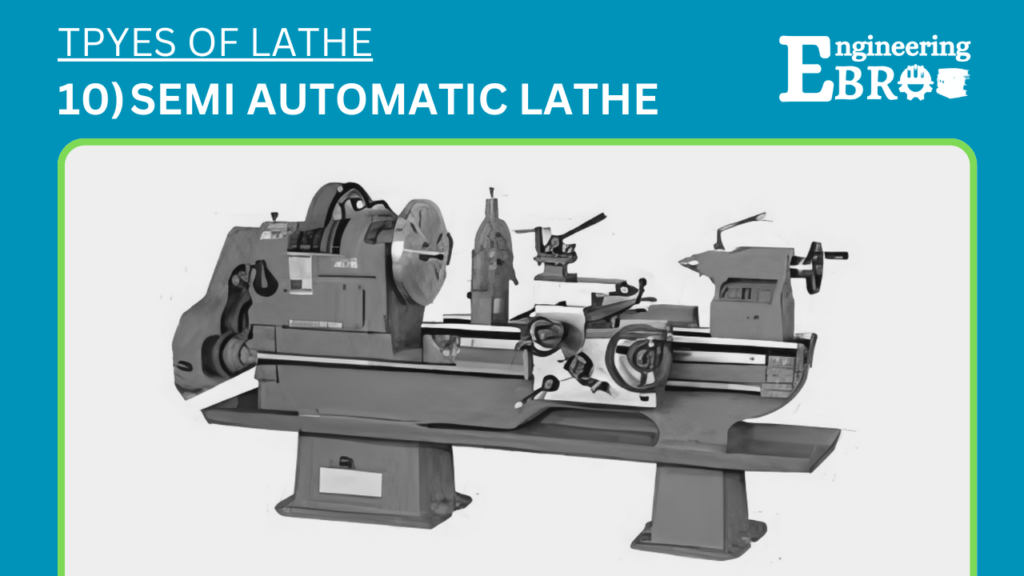
Specifications of a Semi-Automatic Lathe
- Type:
- Semi-automatic, offering both manual and automated operation modes.
- Max Workpiece Diameter:
- Typically ranges from 20 mm to 300 mm, depending on the model and application.
- Max Workpiece Length:
- Generally ranges from 100 mm to 1000 mm.
- Spindle Speed:
- Semi-automatic lathes usually have a wide range of spindle speeds, often from 100 RPM to 3000 RPM, controlled manually or via a variable speed drive.
- Motor Power:
- Motor power ranges from 2 HP to 10 HP, depending on the size and capacity of the lathe.
- Control System:
- May include manual control options along with basic automation features for repetitive tasks.
- Tooling:
- Equipped with manual tool holders or turret tool posts for holding cutting tools.
- Feed Mechanism:
- May include manual feed mechanisms for longitudinal and cross feeds, or semi-automatic feed options for specific operations.
- Construction Material:
- Typically made from high-grade cast iron or steel for stability and vibration reduction.
- Weight:
- Can vary widely, from around 500 pounds to several tons, depending on the size and construction of the lathe.
Frequently asked questions on Types of lathe machines
What are the price ranges of all types of lathe machines available in the market
The estimated price ranges for different types of lathe machines in both Indian Rupees (INR) and US Dollars (USD):
- Engine Lathe:
- INR: ₹3,50,000 to ₹7,00,00,000+
- USD: $5,000 to $100,000+
- Bench Lathe:
- INR: ₹70,000 to ₹70,00,000+
- USD: $1,000 to $10,000+
- Tool Room Lathe:
- INR: ₹7,00,000 to ₹10,50,00,000+
- USD: $10,000 to $150,000+
- Capstan Lathe:
- INR: ₹14,00,000 to ₹21,00,00,000+
- USD: $20,000 to $300,000+
- Turret Lathe:
- INR: ₹21,00,000 to ₹35,00,00,000+
- USD: $30,000 to $500,000+
- Gap Bed Lathe:
- INR: ₹7,00,000 to ₹14,00,00,000+
- USD: $10,000 to $200,000+
- Wheel Lathe:
- INR: ₹3,50,00,000 to ₹70,00,00,000+
- USD: $50,000 to $1,000,000+
- Axle Lathe:
- INR: ₹3,50,00,000 to ₹70,00,00,000+
- USD: $50,000 to $1,000,000+
- Automatic Lathe:
- INR: ₹3,50,00,000 to ₹70,00,00,000+
- USD: $50,000 to $1,000,000+
- Semi-Automatic Lathe:
- INR: ₹3,50,000 to ₹7,00,00,000+
- USD: $5,000 to $100,000+
[top_button]
Why all types of lathe machines are expensive?
All different types of Lathe machines are expensive due to their precision engineering, heavy-duty construction, and advanced features, which ensure reliability, accuracy, and efficiency in machining operations. Additionally, the cost is influenced by factors such as materials used, technological advancements, and market demand for specialized capabilities